O que é SCADA? Controle de supervisão e aquisição de dados explicou
Saiba o que é um sistema SCADA , como funciona, componentes, benefícios e por que SCADA baseado em nuvem está alimentando o Industry 4.0-Guia de Complete em menos de 5 minutos.
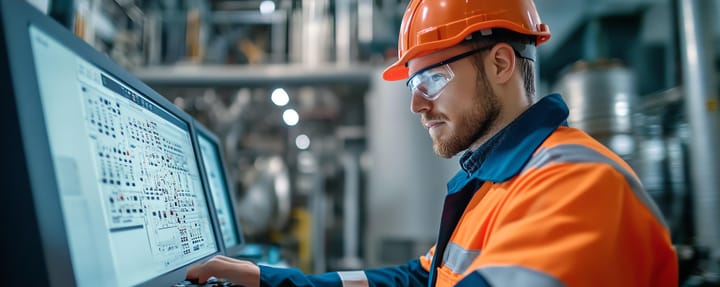
SCADA - Short para controle de supervisão e aquisição de dados - é o centro nervoso da indústria moderna. Pense nisso como um dashboard que observa todas as válvulas, motor e sensor no chão da planta e permite agir antes de uma bolas de neve de soluço no tempo de inatividade.
Na sua essência, um sistema SCADA vincula dispositivos de campo (via PLCS ou RTUs) a um servidor central - agora cada vez mais na nuvem - onde os dados ao vivo são armazenados, visualizados e transformados em informações acionáveis. Os operadores veem temperaturas, pressões e contagens de produção, ajustes de ajuste em tempo real e desencadeiam alertas muito antes de um fracasso custar dinheiro.
Por que isso importa em 2025? Porque os choques da cadeia de suprimentos, os custos de energia e os regs de segurança mais rígidos deixam espaço zero para supor. SCADA bem ajustada ajuda as equipes a esgotar mais a taxa de transferência de ativos envelhecidos, reduzir paradas não planejadas e voltar a todas as decisões com números difíceis. E com SCADA baseado em nuvem , você não precisa mais de racks de servidores ou de uma VPN para acompanhar os sites remotos-apenas um navegador seguro e um bom café.
Neste guia, você aprenderá:
- Como SCADA evoluiu dos mainframes dos anos 70 para soluções de nuvem IoT
- Componentes essenciais - sensores, PLCs, HMIS, bancos de dados - e como eles se encaixam.
- SCADA vs. DCS vs. Plataformas IoT para que você possa escolher o que realmente se encaixa na sua planta.
- Casos de uso do mundo real em energia, água e alimentos e bebidas que comprovam o ROI.
Pronto para levantar o capô na tecnologia que mantém fábricas, oleodutos e grades de energia zumbindo? Vamos mergulhar direto.
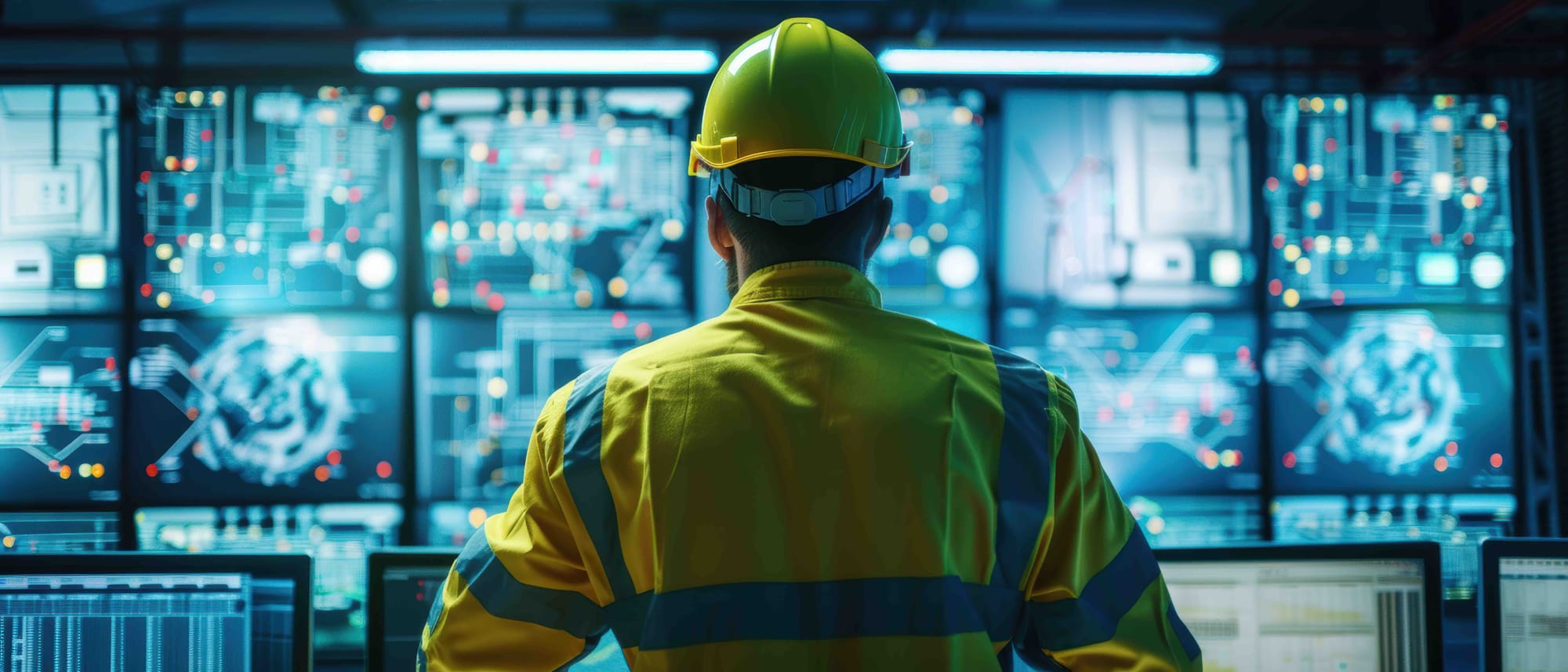
O que é SCADA?
SCADA significa controle de supervisão e aquisição de dados, um termo técnico que se tornou a linha de vida da automação industrial moderna - um sistema de controle composto de componentes de software e hardware que oferece controle total sobre sua operação.
Basicamente, os sistemas SCADA se comunicam diretamente com o maquinário do chão de fábrica, coletando dados em tempo real e disponibilizando-os para sua equipe. Você pode ver o desempenho do equipamento, analisar tendências de dados e detectar ineficiências antes que se tornem grandes problemas. Os sistemas SCADA também facilitam a coleta de dados e a tomada de decisões em tempo real, tornando-os essenciais para o gerenciamento de equipamentos de controle em locais remotos e para melhorar a automação e a eficiência nas operações industriais. O resultado? Mais eficiência, menos gargalos e decisões mais informadas que impactam seus resultados financeiros. Não se trata apenas de manter as rodas girando – trata-se de otimizar cada engrenagem da máquina.
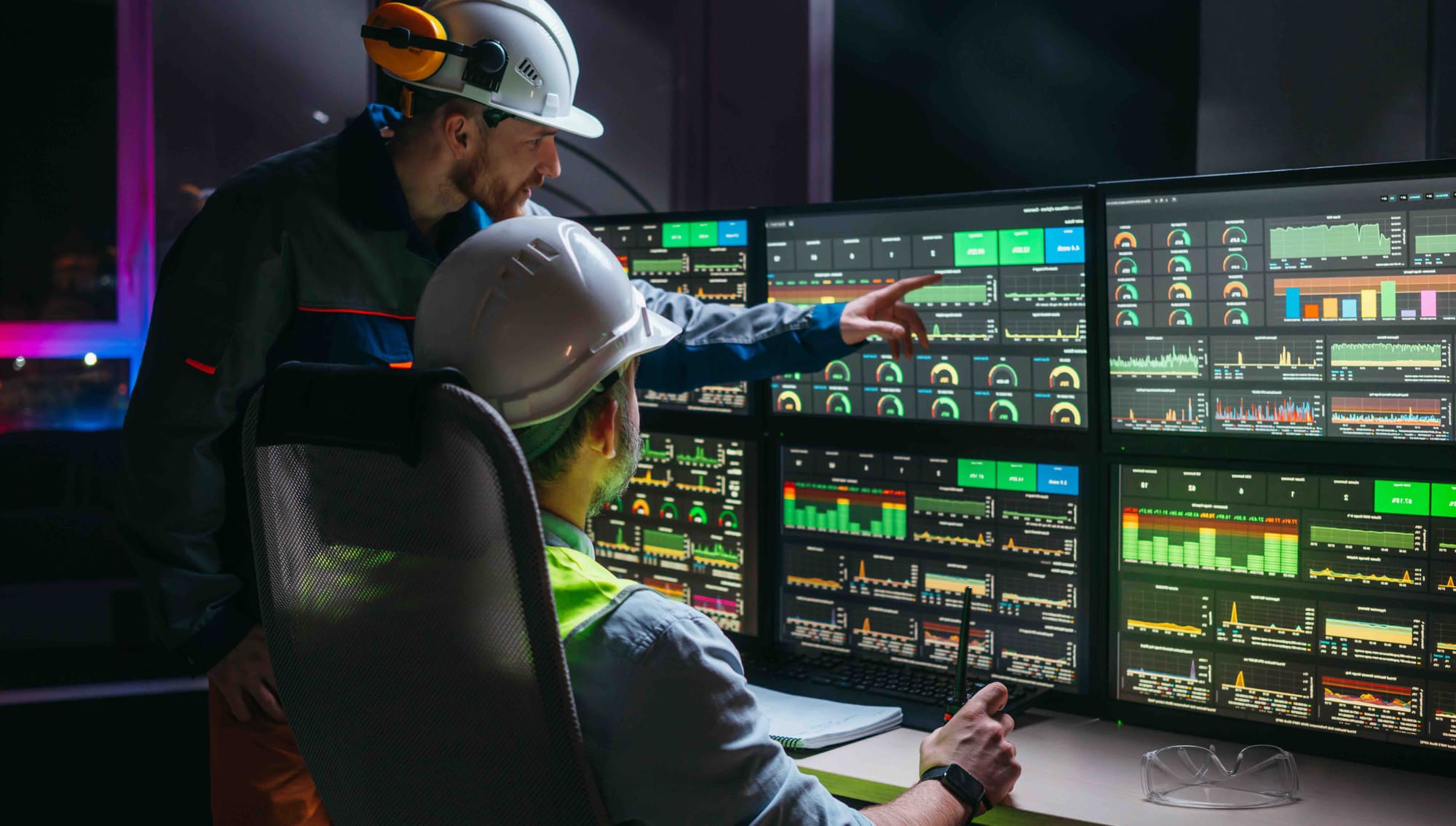
SCADA começa no backbone – controlador lógico programável (PLC) que coleta dados de sensores e dispositivos em toda a planta. Esses CLPs são os tradutores, conversando com objetos como máquinas de fábrica, IHMs (Interfaces Homem-Máquina) e vários dispositivos finais. Eles coletam dados críticos – temperatura, pressão, velocidade e muito mais – e os enviam de volta para um sistema central onde podem ser monitorados, analisados e tratados.
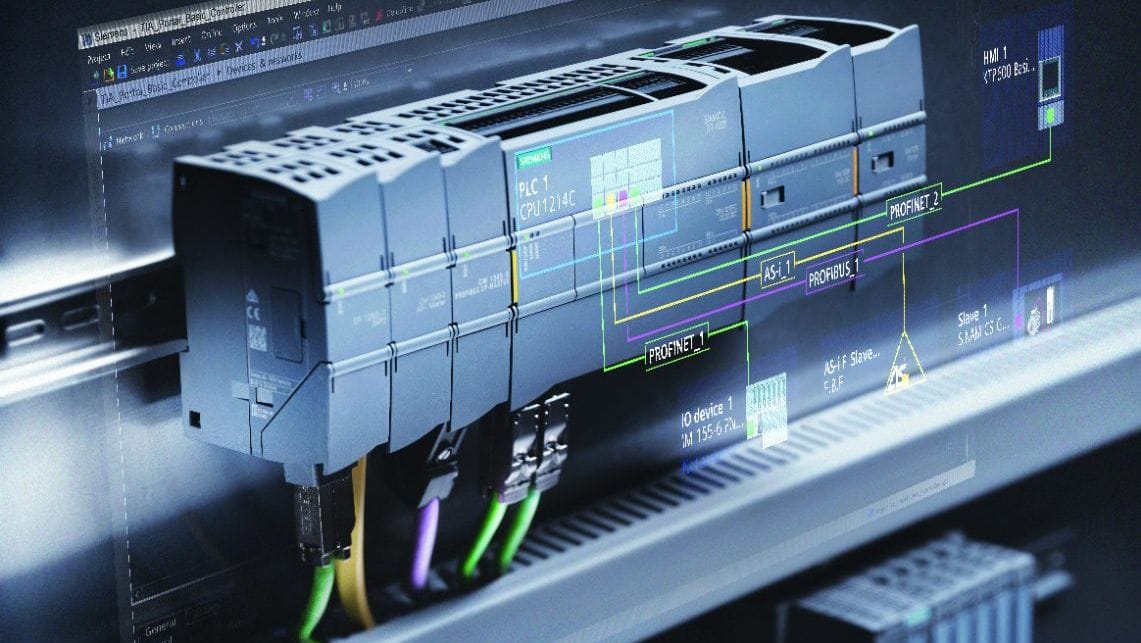
Este nível de granularidade é o que torna SCADA tão essencial. Ele não apenas permite que você veja o que está acontecendo em seus processos, mas também fornece insights para prever problemas antes que eles se transformem em tempo de inatividade.
História e Evolução do SCADA
A história do SCADA começa no início da década de 1970, quando a produção passava por uma grande transformação. O termo SCADA nasceu nesse período e com ele a tecnologia que mudaria a forma como monitoramos e controlamos os processos industriais. Naquela época, tudo começou com computadores mainframe – máquinas enormes que eram o sistema nervoso central dos primeiros sistemas SCADA . Esses mainframes permitiam que as empresas automatizassem algumas funções básicas e coletassem dados críticos, mas isso ainda era desajeitado e limitado pela tecnologia da época.
Primeira Geração
SCADA Monolítico Os primeiros sistemas SCADA foram construídos em computadores mainframe onde todo o processamento estava em uma máquina. Os dados foram coletados, armazenados e processados dentro do mainframe e não havia conectividade de rede entre diferentes sistemas. Esses sistemas SCADA monolíticos eram independentes e o escopo da automação era limitado aos limites físicos da instalação.
Neste ponto, a única forma de controlar (e supervisionar) máquinas era através do uso de circuitos de relés eletromecânicos; cada motor ou atuador teve que ser ligado/desligado individualmente. Isso resultou em fábricas precisando de grandes gabinetes cheios de relés de potência.
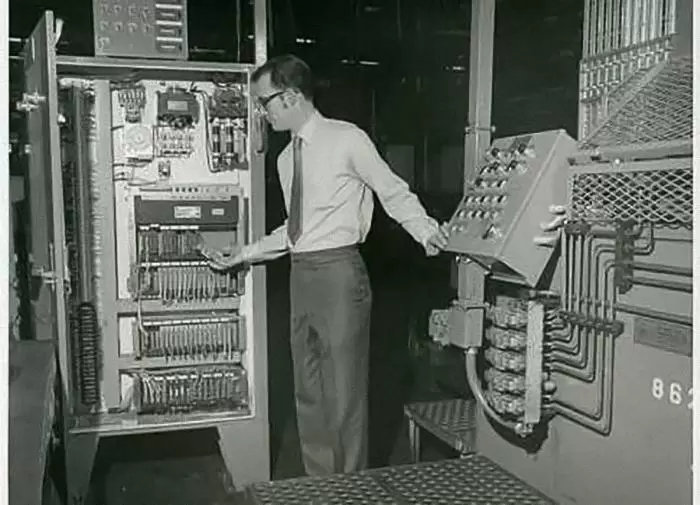
Segunda Geração: O nascimento dos PLCs
Depois vieram os microprocessadores e os controladores lógicos programáveis (CLPs) em meados da década de 70 e nasceu uma nova onda de automação. A capacidade de unificar o controle de processos por meio de PLCs abriu caminho para sistemas de supervisão centralizados e o cenário SCADA começou a mudar. As décadas de 80 e 90 viram SCADA evoluir ainda mais com o desenvolvimento da tecnologia de rede local (LAN) e o surgimento do software de interface homem-máquina (HMI) baseado em PC. Esses sistemas SCADA distribuídos reduziram o espaço ocupado pelo hardware e aumentaram os recursos de comunicação para que os sistemas pudessem se tornar mais modulares, escaláveis e fáceis de usar. Os operadores agora podiam controlar operações complexas da planta a partir de PCs desktop. Desde então, surgiram sistemas SCADA modernos, permitindo acesso a dados em tempo real, melhor integração com outras infraestruturas de TI, como bancos de dados SQL, e oferecendo melhorias significativas em eficiência, segurança e confiabilidade.
Terceira Geração: Sistemas SCADA em Rede
Na década de 90, SCADA começou a aproveitar a rede de longa distância (WAN) e podia se comunicar por longas distâncias. Esses sistemas SCADA em rede adotaram uma arquitetura de sistema aberto e protocolos de comunicação padrão, permitindo a interoperabilidade entre dispositivos de diferentes fornecedores. Isto foi um grande negócio para indústrias como Energia, Petróleo e Gás, que precisavam monitorar vastas e remotas linhas de energia ou oleodutos. Os dados agora poderiam ser enviados para salas de controle distantes do local de operações e centralizar o controle dos sistemas distribuídos.
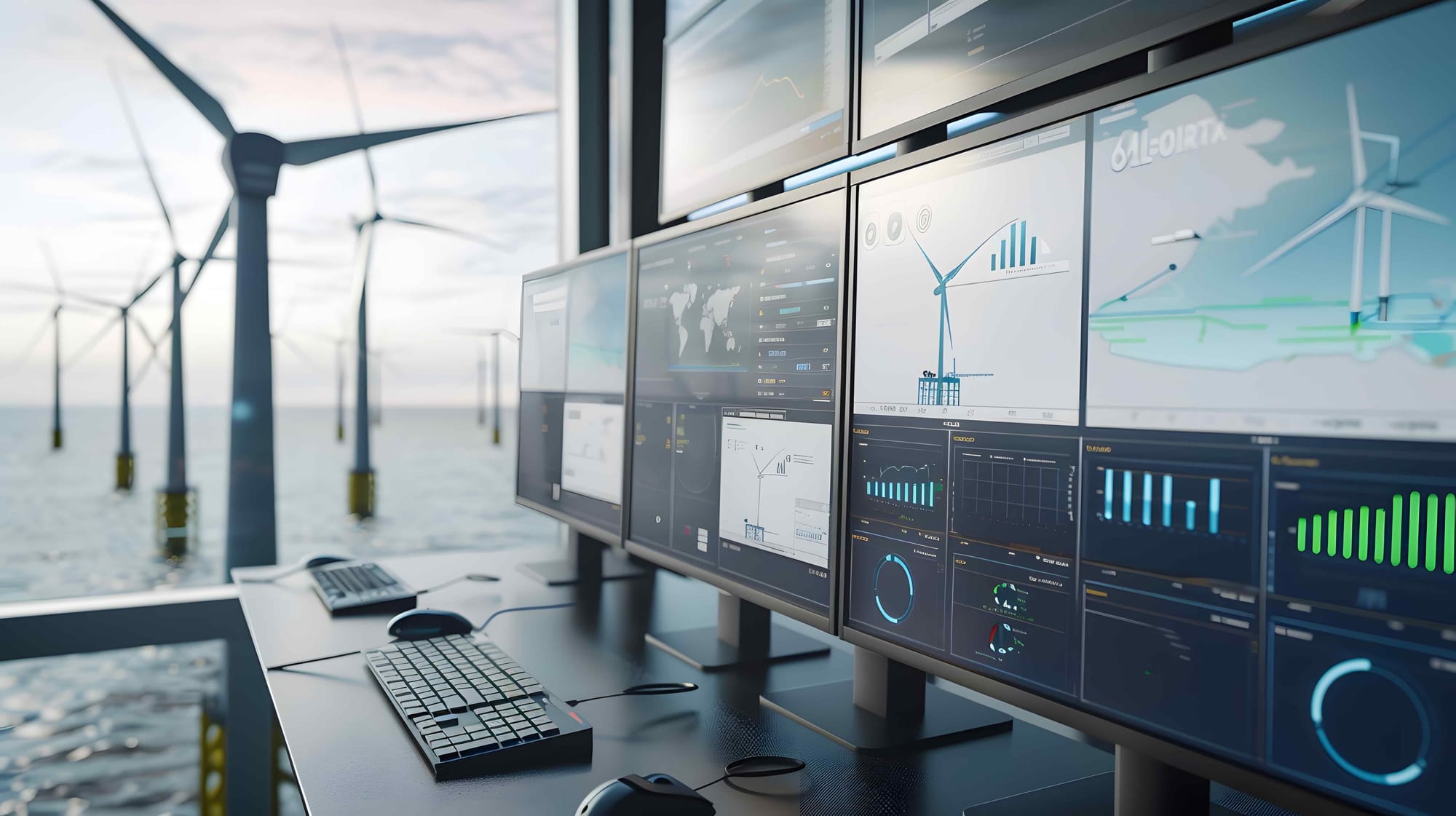
À medida que entrámos no século XXI, os sistemas SCADA abraçaram a análise de dados em tempo real, a computação em nuvem e a conectividade global. Os sistemas atuais estão muito longe dos mainframes antigos, com dados fluindo do chão de fábrica para as salas de controle (e além) em tempo real. Na verdade, as plataformas SCADA modernas permitem o monitoramento remoto de qualquer lugar do mundo – esteja você em sua mesa ou em trânsito. Assim, os gerentes de confiabilidade não precisam mais ficar presos às suas estações de trabalho para manter o controle de suas operações. Com apenas alguns cliques eles podem ver o status do equipamento, diagnosticar problemas e tomar decisões rapidamente.
A próxima evolução para sistemas SCADA
A próxima evolução dos sistemas SCADA está sendo moldada pelo surgimento de plataformas SCADA e IIoT baseadas em nuvem. Essas tecnologias estão permitindo uma mudança de sistemas tradicionais locais para soluções mais flexíveis, escaláveis e remotas. SCADA baseado em nuvem permite que dados em tempo real sejam acessados de qualquer lugar, oferecendo visibilidade e controle sem precedentes sobre as operações. Juntamente com as plataformas IIoT , que integram uma vasta rede de sensores e dispositivos inteligentes, os sistemas SCADA estão se tornando mais conectados e ricos em dados. Esta evolução proporciona às indústrias uma visão mais profunda dos seus processos, permitindo uma tomada de decisão mais rápida e uma gestão proativa de equipamentos e recursos, ao mesmo tempo que reduz os custos de infraestrutura e aumenta a eficiência operacional.
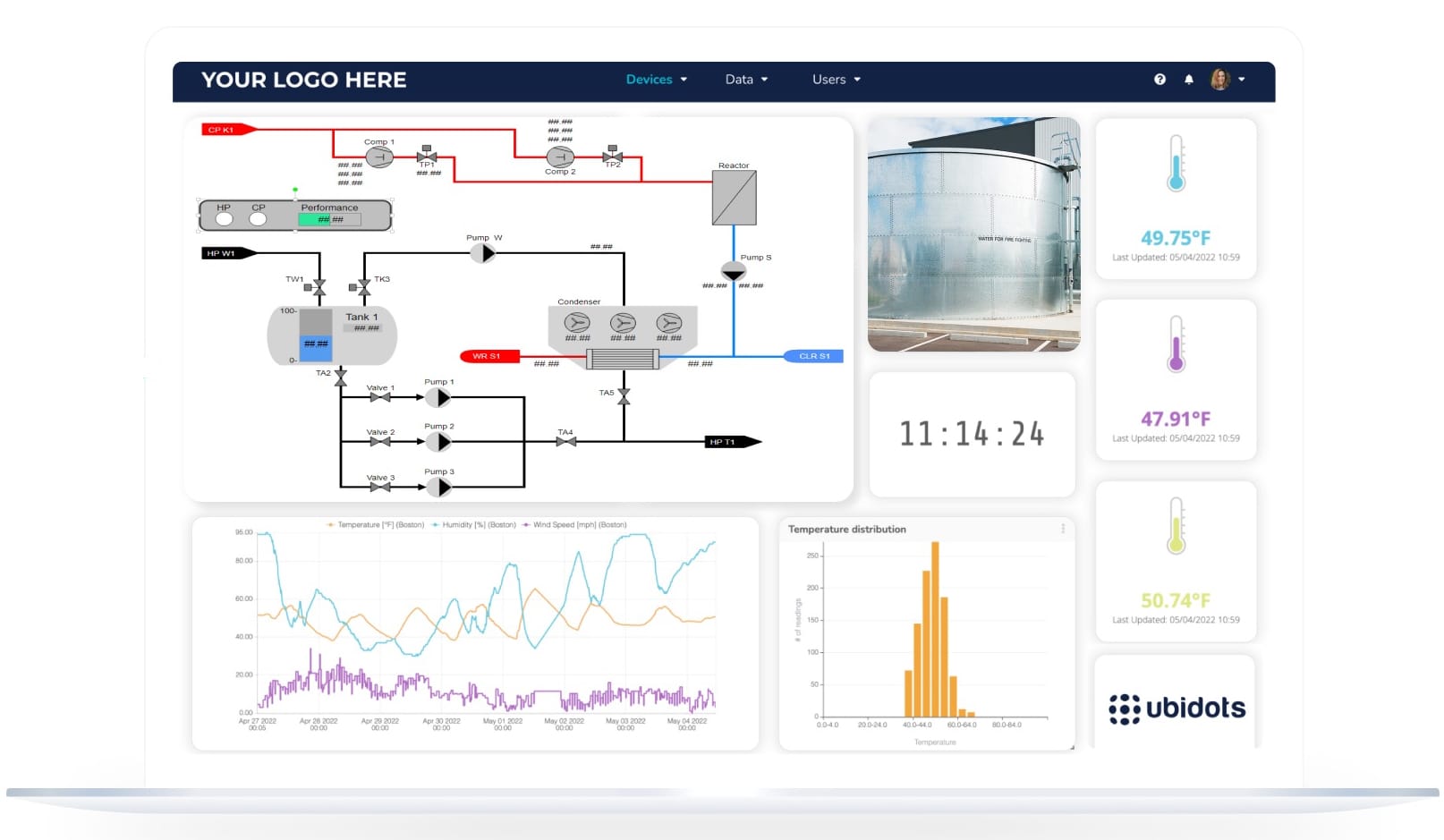
Componentes SCADA
No coração de cada sistema SCADA estão os seus componentes – cada um desempenhando um papel crítico no controle e monitoramento de processos industriais complexos. Esses componentes trabalham juntos para oferecer aos gerentes de confiabilidade total visibilidade e controle de seus equipamentos a quilômetros de distância:
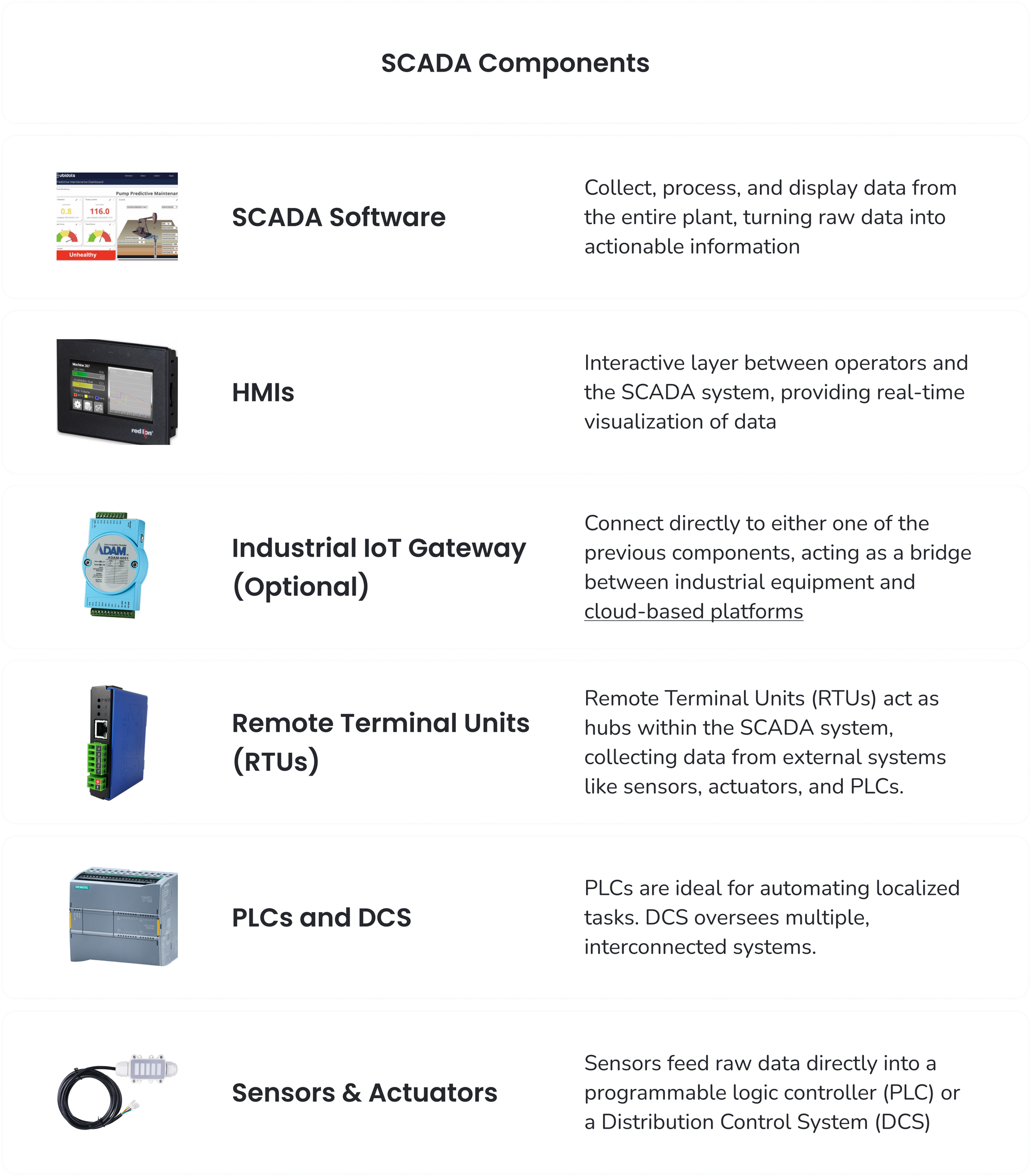
1- Sensores e Atuadores
Tudo começa no terreno com sensores e atuadores. Quer se trate de temperatura, pressão, taxas de fluxo ou velocidade do motor, os sensores coletam e transmitem dados em tempo real sobre o estado atual dos equipamentos e processos usando protocolos de comunicação como Modbus , HART e Profibus . Os atuadores, por sua vez, recebem comandos do sistema de controle utilizando os mesmos protocolos para ajustar processos físicos, como abertura de uma válvula ou partida de um motor, garantindo que o sistema opere dentro dos parâmetros desejados.
2- Controladores Lógicos Programáveis (CLPs) e Sistemas de Controle de Distribuição (DCS)
Controladores lógicos programáveis (CLPs) e sistemas de controle de distribuição (DCS) servem como o “cérebro” do sistema, mas diferem em escala e função. Os PLCs, muitas vezes comunicando-se via Modbus , Ethernet/IP ou Profibus , são normalmente usados para controle discreto e são ideais para automatizar tarefas localizadas, como controlar uma única máquina em uma linha de montagem. O DCS, que normalmente usa OPC-UA , Foundation Fieldbus ou Modbus TCP/IP , é projetado para processos contínuos e supervisiona vários sistemas interconectados em uma instalação maior, como uma fábrica de produtos químicos. Por exemplo, enquanto um PLC pode controlar o arranque e a paragem de motores numa linha de produção, um DCS geriria todo o processo de produção contínua de uma refinaria de petróleo, garantindo uma coordenação perfeita entre vários subsistemas.
3- Unidades Terminais Remotas (RTUs)
Como o nome sugere, este componente é comum em aplicações remotas. As UTRs atuam como hubs de dados dentro do sistema SCADA , colocados em fábricas ou locais remotos para coletar e transmitir dados de sistemas externos, como sensores, atuadores e PLCs. As RTUs são usadas em vários setores e os protocolos de comunicação que empregam podem variar dependendo da aplicação específica:
- Fabricação : Em configurações de fabricação industrial, as RTUs geralmente usam Modbus RTU ou Modbus TCP/IP para comunicação confiável entre máquinas e sistemas de controle. Esses protocolos são amplamente suportados por dispositivos industriais, permitindo integração perfeita com PLCs e sensores no chão de fábrica.
- Petróleo e Gás : Para monitoramento remoto de oleodutos, cabeças de poço e refinarias, DNP3 e IEC 60870-5-101/104 são comumente usados devido ao seu desempenho robusto em comunicações de longa distância e ambientes agressivos. Esses protocolos garantem que os dados sejam transmitidos de forma confiável de locais remotos para a sala de controle, muitas vezes em amplas áreas geográficas.
- Gestão de Água e Águas Residuais : DNP3 e Modbus são frequentemente usados em sistemas de gestão de água por sua capacidade de suportar monitoramento e controle remoto de bombas, válvulas e estações de tratamento. A confiabilidade e a facilidade de implementação tornam esses protocolos ideais para sistemas distribuídos, como instalações de água e esgoto.
- Setor de Energia : A indústria de energia normalmente depende da IEC 60870-5-101/104 e DNP3 , que são projetadas para alta confiabilidade e segurança em redes de transmissão e distribuição de energia. Esses protocolos suportam monitoramento em tempo real de subestações, transformadores e outras infraestruturas críticas em grandes redes de serviços públicos.
As UTRs coletam dados em tempo real de sensores e atuadores, convertem-nos em um formato adequado para sistemas SCADA e transmitem-nos para um software SCADA central ou Interface Homem-Máquina (HMI) para processamento e controle adicionais. Além disso, as RTUs podem enviar comandos de volta aos dispositivos de campo, permitindo o controle remoto de equipamentos, mesmo em operações grandes ou geograficamente dispersas. Isto torna as RTUs essenciais para indústrias que exigem monitoramento e controle em tempo real em ambientes distribuídos.
3.1 Gateway IoT Industrial (Opcional)
Os Gateway IoT Industriais podem servir como uma adição opcional, mas altamente valiosa, aos sistemas SCADA Esses gateway podem se conectar diretamente a qualquer um dos componentes mencionados acima – sensores/atuadores, PLCs ou RTUs – atuando como uma ponte entre equipamentos industriais e plataformas baseadas em nuvem . Por um lado, eles podem suportar protocolos industriais como OPC-UA , Modbus , PROFINET , EtherNet/IP e BACnet , garantindo compatibilidade com uma ampla gama de dispositivos e máquinas. Por outro lado, eles retransmitem dados usando protocolos compatíveis com a nuvem, como HTTP e MQTT , facilitando a troca de dados segura e eficiente entre o chão de fábrica e a nuvem. Essa combinação permite a coleta de dados em tempo real, o monitoramento remoto e análises avançadas, permitindo que as empresas otimizem as operações e aproveitem soluções baseadas em nuvem para manutenção preditiva e transformação digital.
4- Interfaces Homem-Máquina (IHMs)
As interfaces homem-máquina (HMIs) servem como camada interativa entre os operadores e o sistema SCADA , fornecendo visualização em tempo real de dados coletados de sistemas externos, como PLCs, RTUs e sensores. As IHMs podem estar localizadas em uma sala de controle centralizada, onde os operadores monitoram e gerenciam toda a instalação, ou posicionadas localmente próximas a um CLP ou processo específico para controle no local. Em configurações centralizadas, as IHMs permitem que os operadores supervisionem as operações em toda a planta e emitam comandos remotamente. Em configurações locais, permitem que os técnicos interajam diretamente com máquinas ou processos específicos no chão de fábrica, ajustando parâmetros ou respondendo a alarmes em tempo real. Esta flexibilidade garante que os operadores tenham o nível certo de controle, quer estejam gerenciando toda a planta ou concentrando-se em uma única máquina.
5- Software SCADA
E, finalmente, as soluções de software SCADA , como o software Ignition , são o que reúne tudo isso. Essas soluções poderosas coletam, processam e exibem dados de toda a planta, transformando dados brutos em informações acionáveis. Através de análise de tendências, alarmes e dados históricos, o software SCADA ajuda operadores e gerentes a tomar decisões para melhorar a eficiência, reduzir o tempo de inatividade e prevenir problemas antes que se tornem problemas. É a torre de controle de toda a operação, proporcionando não apenas uma visão do que está acontecendo agora, mas também análises preditivas para se preparar para o que está por vir.
Cada um desses componentes é crítico para um sistema SCADA . Sem eles, você estaria voando às cegas em um mundo orientado por dados. Juntos, eles fazem sua operação funcionar como uma máquina bem lubrificada, com o mínimo de soluços e a máxima eficiência.
Escolhendo o sistema SCADA certo
Escolher o sistema SCADA certo para sua operação é uma decisão que terá impacto na eficiência, segurança e crescimento de sua planta a longo prazo. Com tantas opções disponíveis, é importante pesar os principais fatores que afetarão não apenas o desempenho imediato, mas também a escalabilidade e adaptabilidade do sistema à medida que suas instalações evoluem.
Interface do usuário: mantenha a simplicidade
Uma das partes mais importantes de qualquer sistema SCADA é a interface do usuário (UI). Se seus operadores não conseguirem navegar facilmente no sistema, todas as funcionalidades avançadas do mundo não terão importância. Procure um sistema que tenha uma UI limpa e intuitiva, dashboards claros e navegação simples. Quando os alarmes disparam ou são necessários ajustes rápidos, a última coisa que você deseja é uma interface de usuário confusa e desordenada que retarda a tomada de decisões.
Uma boa interface SCADA permite que sua equipe trabalhe com eficiência, tome decisões em tempo real e reduza erros humanos, fatores críticos em ambientes de alta pressão.
Escalabilidade: seu sistema à prova de futuro
As operações industriais nunca são estáticas. À medida que sua empresa cresce, seu sistema SCADA deve crescer junto. A escalabilidade é um fator chave na escolha de uma plataforma SCADA . Esteja você adicionando novas instalações ou linhas de produção, seu sistema SCADA deverá ser capaz de lidar com maiores cargas de dados, mais sensores e novos processos.
Um sistema que possa se adaptar a mudanças futuras evitará que você precise de atualizações ou substituições dispendiosas no futuro. Pense no longo prazo não apenas nas suas necessidades atuais, mas também em como você vê a evolução da sua operação nos próximos 5 a 10 anos.
Compatibilidade: Integração com Protocolos Industriais
Seu sistema SCADA precisará se comunicar com muitos dispositivos e máquinas no chão de fábrica. É importante escolher um sistema que seja compatível com protocolos industriais comuns como Modbus, DNP3 e OPC UA. Compatibilidade significa que seu sistema SCADA pode ser integrado a equipamentos existentes e a qualquer nova tecnologia que você possa adicionar.
Essa interoperabilidade também permite que seu sistema extraia dados de diversas fontes, proporcionando uma visão holística de sua operação. Sem a compatibilidade adequada, você terá soluções alternativas dispendiosas e dados fragmentados que retardam a eficiência operacional.
Segurança: proteja sua infraestrutura
À medida que os sistemas SCADA se conectam às soluções baseadas na web e na nuvem, a segurança se torna uma prioridade máxima. Garantir que seu sistema SCADA atenda aos padrões de segurança exigidos pelo seu departamento de TI não é negociável. Você vai querer perguntar a seus fornecedores em potencial sobre seus protocolos de segurança, padrões de criptografia, autenticação multifator e como eles lidam com patches ou vulnerabilidades.
No mundo de hoje, uma violação de segurança pode ser devastadora – não apenas financeiramente, mas também para a sua força de trabalho e para o meio ambiente. Escolha um fornecedor que torne a segurança uma parte essencial de seus negócios e não uma reflexão tardia.
Confiabilidade do fornecedor: um parceiro de longo prazo
Quando se trata de SCADA seu relacionamento com o fornecedor não termina após a instalação. A confiabilidade do fornecedor é fundamental para o sucesso do seu sistema a longo prazo. Você quer um fornecedor com histórico comprovado de sustentabilidade e suporte ao cliente. Eles devem estar por perto para apoiá-lo com atualizações do sistema, solução de problemas e expansões.
Pesquise a reputação do fornecedor no setor, analise estudos de caso e peça depoimentos. Um fornecedor confiável será um parceiro para ajudá-lo a evoluir e manter seu sistema SCADA nos próximos anos.
Orçamento: Planejando o crescimento sem exageros
Embora seja fácil optar pelo sistema SCADA mais avançado que existe, você precisa equilibrar seu orçamento com as necessidades de sua planta. Alguns sistemas podem ter recursos que são exagerados para operações menores. Optar por um sistema caro e complexo irá prendê-lo a custos desnecessários.
Cuidado também com custos ocultos – especialmente serviços profissionais. Os fornecedores podem cobrar extra por modificações ou expansões. Obtenha uma compreensão clara de quanto custarão os serviços contínuos para que você possa orçamentá-los. Planejar o crescimento sem se comprometer demais com um sistema que se tornará muito caro com o tempo é fundamental para ser ágil e evitar a dependência de fornecedores.
Escolher o sistema SCADA certo é uma grande decisão, mas com um planejamento cuidadoso e considerando esses fatores, você estará pronto para tomar uma decisão que impulsione a eficiência operacional, proteja seus dados e escale com seu negócio.
Opções de software SCADA
Ignition SCADA: a escolha moderna e flexível para fabricantes
Ignition SCADA se tornou uma solução SCADA moderna para fabricantes por sua flexibilidade e arquitetura aberta. Ao contrário dos sistemas SCADA tradicionais, Ignition possui tags, clientes e conexões ilimitadas para que você obtenha a escalabilidade necessária sem custos. Sua moderna interface baseada na web permite acesso a partir de qualquer dispositivo, dados em tempo real e controle na ponta dos dedos. O design modular significa que você pode começar pequeno e crescer conforme necessário, integrando-se com sistemas e protocolos existentes, tornando-se a escolha flexível para fabricantes que buscam preparar suas operações para o futuro.
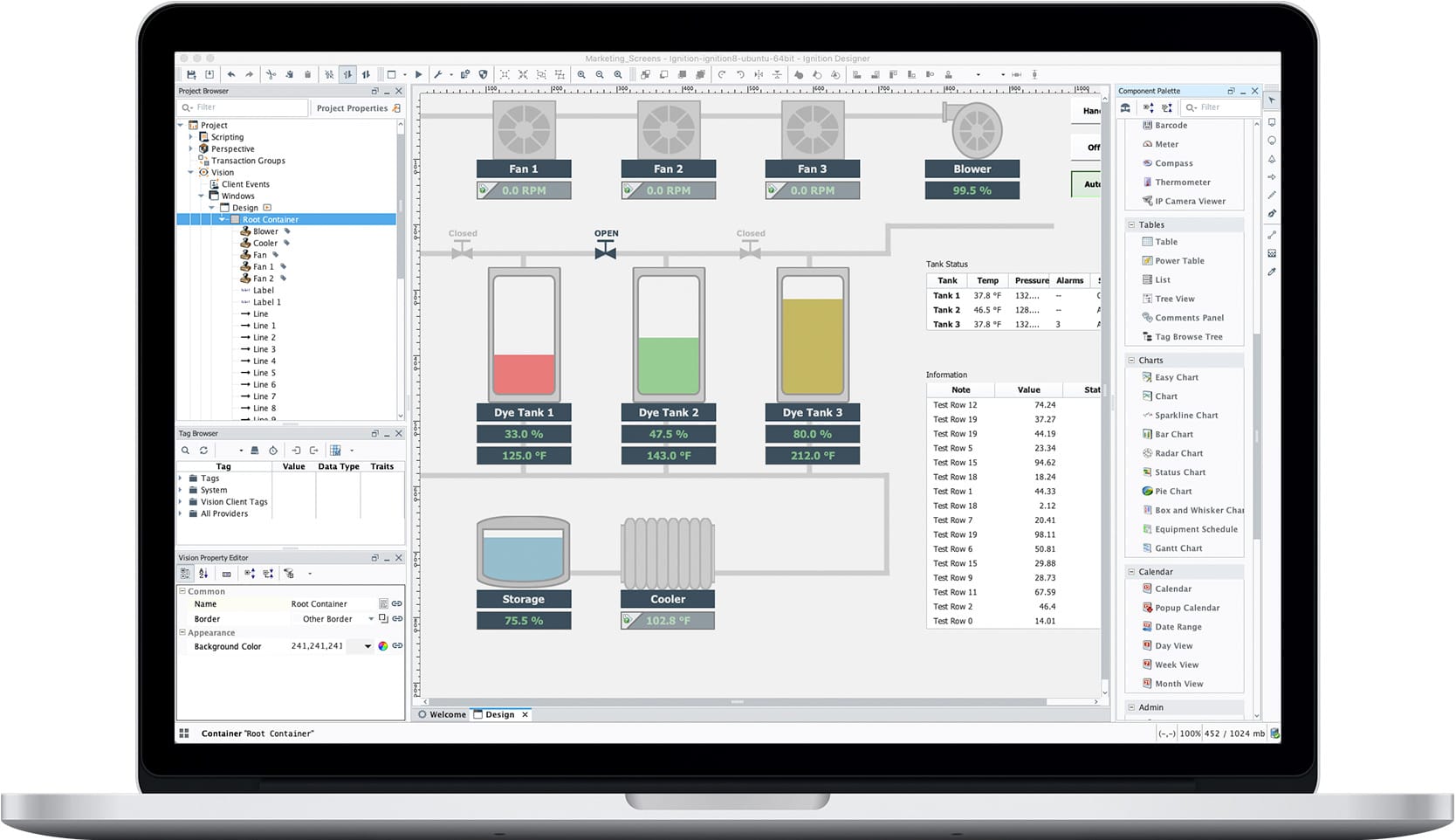
Siemens SCADA - Simatic WinCC: avançado para indústrias complexas
O Siemens SCADA, particularmente o Simatic WinCC, é de alto desempenho, monitoramento e controle em tempo real, por isso é perfeito para grandes indústrias complexas. Do setor farmacêutico à energia, os sistemas SCADA da Siemens oferecem precisão incomparável com ampla funcionalidade para visualização de processos, aquisição de dados e manutenção preditiva. A integração do Simatic WinCC com os produtos de automação da Siemens cria um ambiente contínuo onde PLCs, IHMs e SCADA conversam entre si. Para fábricas onde o tempo de atividade é crítico e o tempo de inatividade pode custar milhões, o Siemens SCADA oferece confiabilidade e recursos avançados para agilizar até mesmo as operações mais complexas.
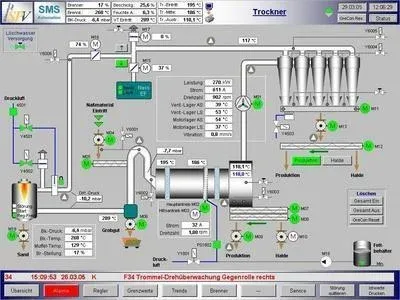
Schneider SCADA: uma alternativa abrangente
A Schneider Electric fornece um conjunto robusto de soluções SCADA e de telemetria, oferecendo componentes de hardware e software para otimizar o controle e o monitoramento. Sua linha de hardware inclui unidades terminais remotas (RTUs), controladores lógicos programáveis (PLCs) e gatewayde comunicação, que são projetados para integração perfeita em ambientes industriais existentes. No lado do software, a Schneider oferece plataformas SCADA avançadas, como o EcoStruxure, que permitem a aquisição de dados em tempo real, a monitorização remota e a análise preditiva, permitindo às empresas agilizar as operações e, ao mesmo tempo, melhorar a gestão energética e a sustentabilidade. Com estas soluções abrangentes, a Schneider pode ser um parceiro confiável para requisitos atuais e futuros.
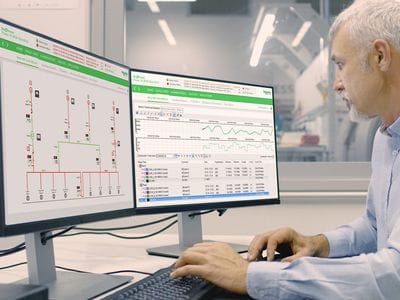
Wonderware SCADA: comprovado para controle de supervisão
A Wonderware, que também faz parte do portfólio da Schneider Electric após a aquisição da Invensys em 2014, tem um longo legado no fornecimento de soluções SCADA confiáveis para uma ampla gama de indústrias. A Wonderware evoluiu para uma plataforma confiável em setores como montagem automotiva, alimentos e bebidas, energia e gerenciamento de água. A adaptabilidade e facilidade de integração do Wonderware com sistemas industriais fazem dele uma solução ideal para melhorar a eficiência operacional e a confiabilidade.
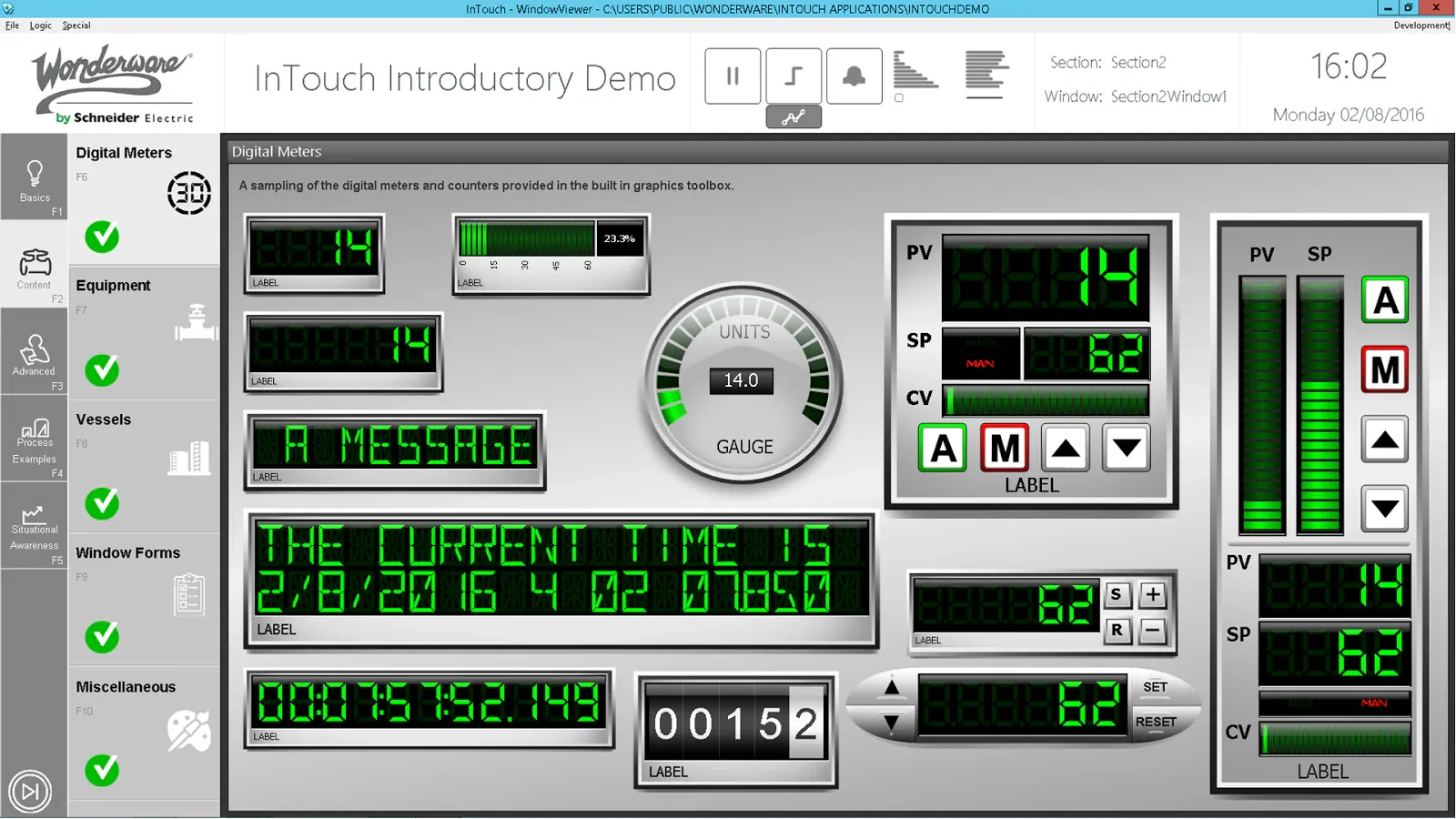
SCADA AVEVA: Cloud SCADA para Indústria 4.0
SCADA A AVEVA se estabeleceu como líder em soluções SCADA baseadas em nuvem, impulsionando a transformação digital em todos os setores. Em 2023, a AVEVA foi adquirida pela Schneider Electric, fortalecendo o portfólio da Schneider para fornecer soluções de fábrica inteligentes. Com sua abordagem cloud-first, a AVEVA permite monitoramento e controle remotos, permitindo que as empresas otimizem as operações em qualquer lugar do mundo. Indústrias como energia, petróleo e gás e gestão de água contam com o software SCADA da AVEVA para aumentar a eficiência e a sustentabilidade.
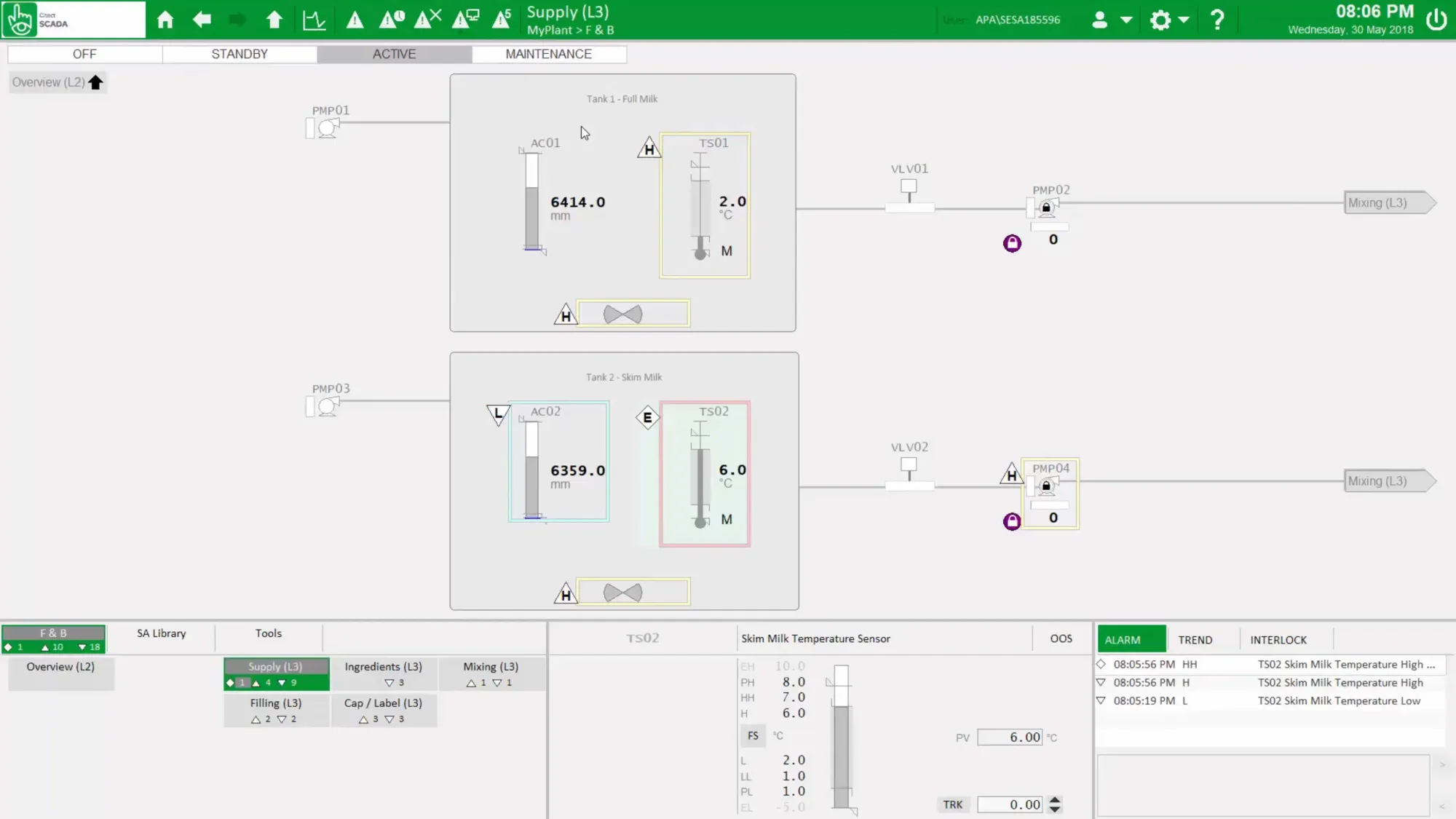
VT SCADA: um nome para monitoramento e controle remoto
Embora seja um player menor, o VT SCADA ganhou participação de mercado em setores que exigem monitoramento e controle remoto robusto, entre outros. Seu modelo de licenciamento simples e desempenho confiável o tornam uma escolha popular para estações de tratamento de água, oleodutos e serviços públicos. O VT SCADA foi projetado para alta disponibilidade com recursos como redundância integrada e failover automático para que os sistemas permaneçam ativos mesmo em condições adversas. Ele pode ser executado em ambientes remotos e distribuídos com manutenção mínima, portanto o VT SCADA é a melhor escolha para setores onde a visibilidade remota em tempo real é crítica para a continuidade dos negócios.
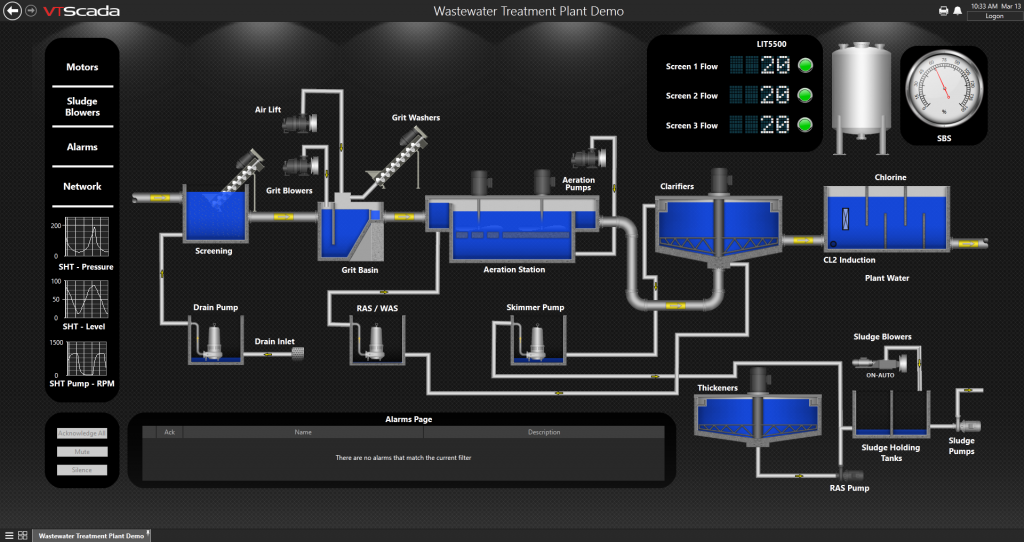
Conclusão
Escalabilidade e flexibilidade: as chaves para a transformação digital
No mundo industrial em rápida mudança de hoje, a escalabilidade e a flexibilidade são mais do que apenas palavras – são a base do crescimento. Um SCADA que pode ser dimensionado de acordo com sua operação significa que você não ficará preso a tecnologias antigas quando seu negócio crescer. Seja adicionando novas linhas de produção, mais dispositivos IoT ou fluxos de dados complexos, um SCADA deve ser capaz de lidar com demandas crescentes sem esforço. A flexibilidade também é fundamental, pois cada setor é diferente. A capacidade de personalizar o sistema de acordo com seu fluxo de trabalho operacional e integrá-lo aos protocolos existentes é a chave para preparar sua estratégia de automação para o futuro.
Cloud SCADA: o complemento perfeito para sistemas SCADA legados
Cloud SCADA não é mais um conceito – está se tornando a nova norma no mundo industrial. Com acesso a dados em tempo real de qualquer lugar do mundo, SCADA na nuvem oferece flexibilidade operacional sem precedentes. A nuvem elimina a necessidade de infraestrutura local, reduzindo os custos de manutenção e aumentando a escalabilidade. À medida que a Internet das Coisas Industrial (I IoT ) cresce, SCADA dominará a oferta de mais segurança, integração perfeita com outras ferramentas digitais e agilidade para enfrentar os desafios modernos de fabricação. Para os gerentes de confiabilidade que buscam estar à frente da curva, a transição para um SCADA pode ser o próximo grande passo para otimizar a eficiência e a competitividade.